The pursuit of perfection
800 Series has always been driven by obsession. Back in 1979, the brief to our engineering team gave them absolute free rein to deliver the very best loudspeaker they could, without any of the usual restrictions.
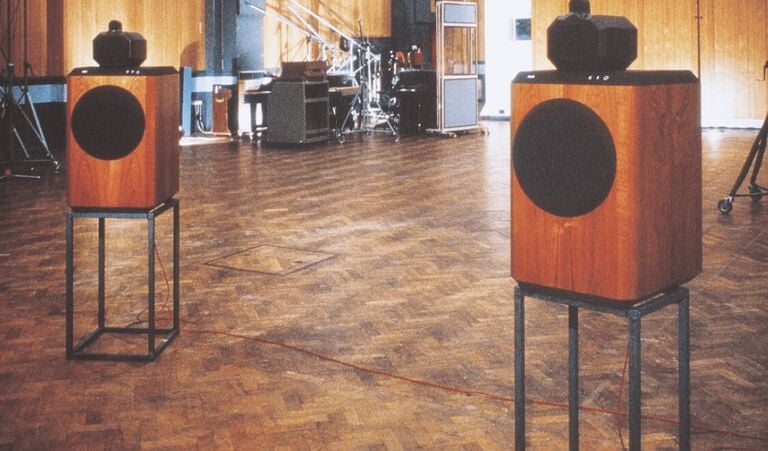
Ask many a designer, and they’ll tell you that most hi-fi products are a compromise, taking into consideration factors such as budgets, aesthetics, production limitations and so on. The art of the engineer and designer is to come up with the best possible product within those limits, while still creating something commercial enough to find a market.
But when the original Bowers & Wilkins 801 speakers were designed, all such thinking went out of the window: the brief to the engineers was absolute free rein to develop the very best loudspeaker they could, without any of the usual restrictions.
That’s made clear in the manual accompanying the speakers when they were launched in 1979: it describes them as ‘the first commercial effort to develop and produce a loudspeaker that would reflect the highest standards attainable without regard to any of the so called “practical considerations” that inevitably compromise conventional designs.’
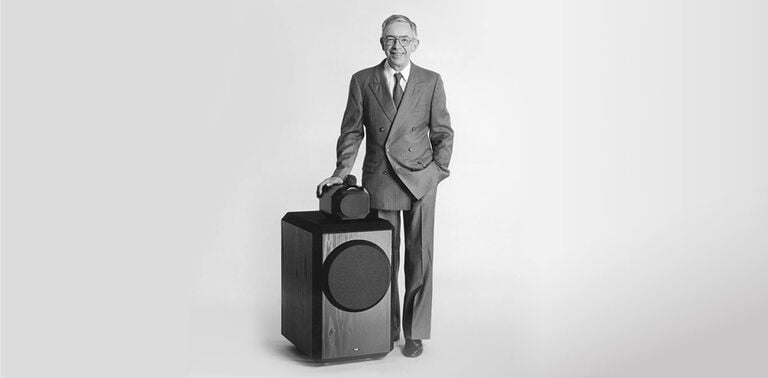
In that statement, the 801 epitomised the founding principles of the company: John Bowers started making speakers simply because he believed he could do better than the models then on the market, and his greatest achievement yet, the 801, would set the bar for just about every Bowers & Wilkins speaker to follow. It was the result of four years’ research, involving the development of new thinking in measurement, design, and production technology, all of which has gone on to be the mainstay of everything the company does.
Fundamental to all that work was the then-innovative use of computer modelling and analysis: these days it’s a mainstay of loudspeaker design, but when the 801 was being developed back in the 1970s it was unheard of, as was the concept of ‘numerical optimisation’ in place of plenty of trial and error. At the time, it was explained that ‘by measuring and comparing a working model of the crossover network with the computer model…we were able to achieve a very high order of correspondence between ideal and real-world function.’
Innovative, too, was the use of laser interferometry to analyse the movement of drive units.
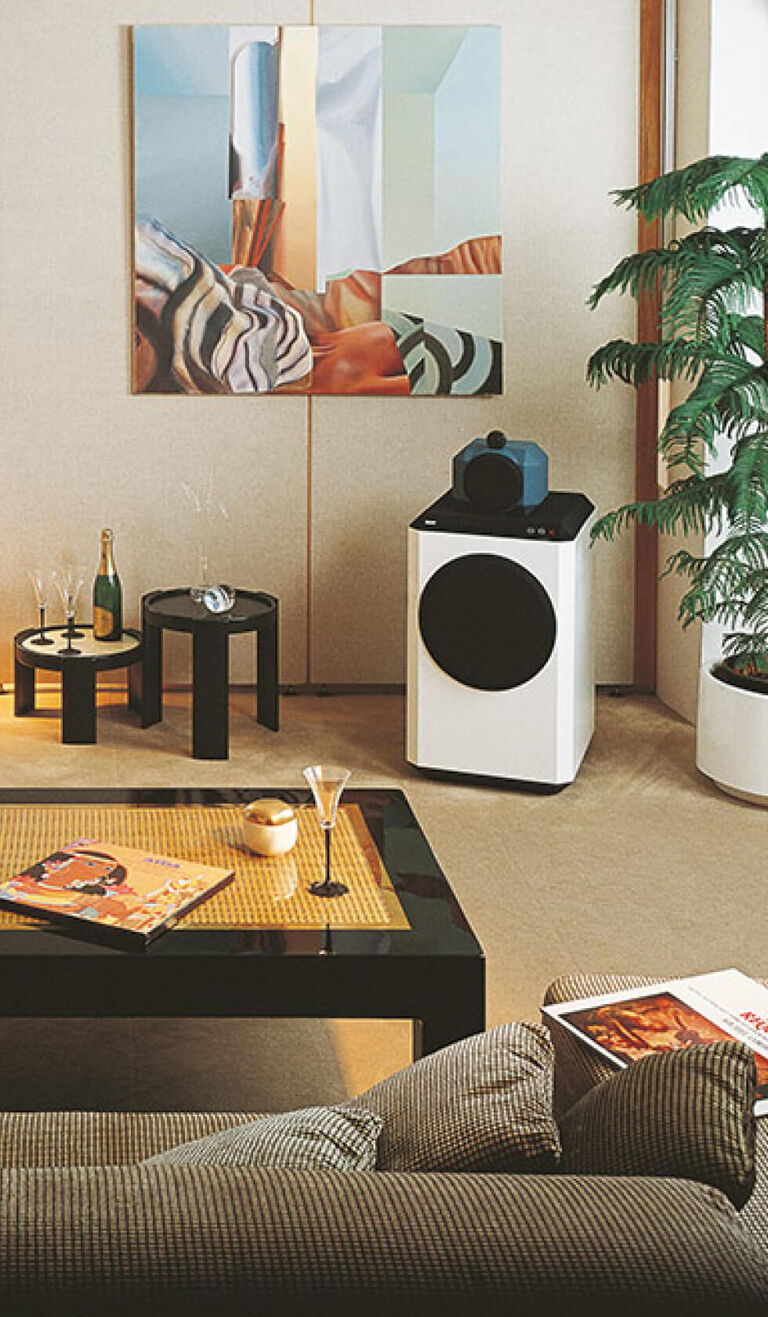
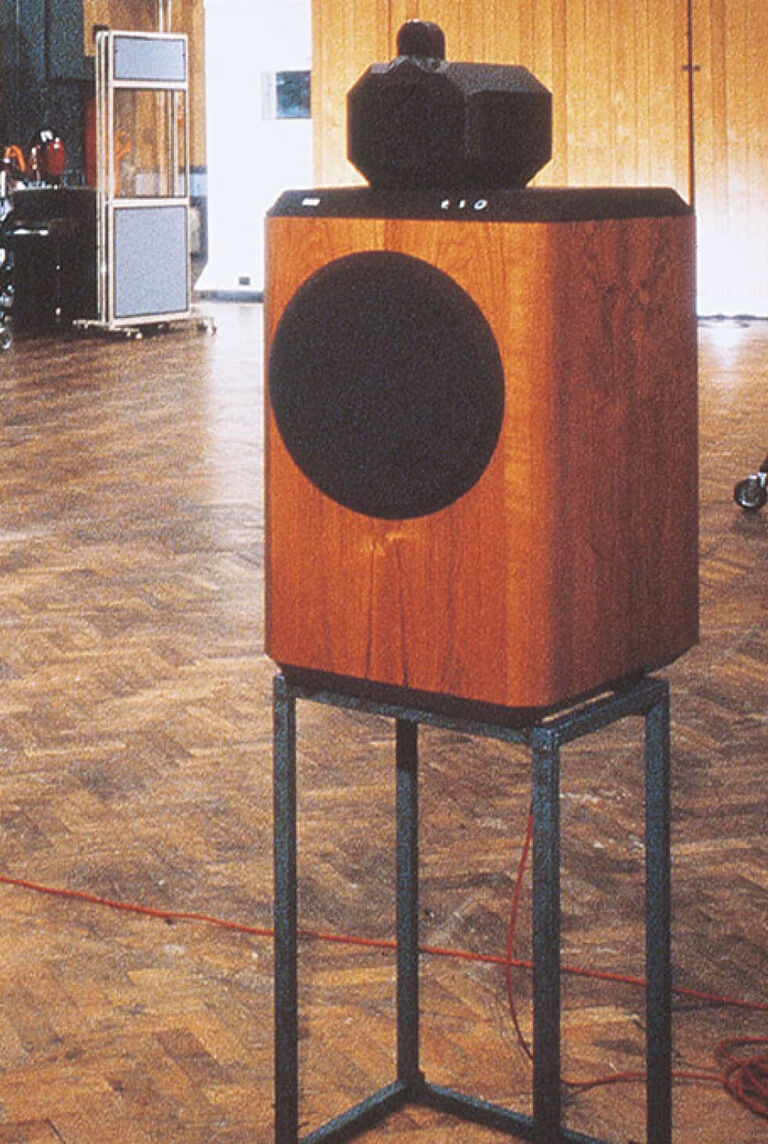
Hardly surprising, then, that the 801 looked unlike anything else on the market, to the extent that an optional foam ‘hood’ was available for those users who thought the ‘form following function’ design looked a bit too functional! While beautifully finished, especially in high-quality wood veneers, the 801 wore its heart on its sleeve with its separate enclosures for the big 27cm woofer, and the 26mm tweeter and 10cm midrange driver – a trend still very much apparent in the current 800 Series Diamond models. This design was something the company had been exploring before the arrival of the 801 in models such as the iconic DM70, with its curved cabinet and separate mid/tweeter enclosure, and the DM7, which pioneered the ‘Tweeter-on-Top’ idea. This isolated the delicate output of the treble driver from the rest of the speaker by mounting the tweeter in a separate pod (a design element still found across the range). However, the 801 is where all that innovative thinking came together.
That big bass module was a sealed box, keeping the bass entirely controlled wherever the speaker was placed, while the engineers’ willingness to explore new materials in the quest for better performance was evident in that treble/midrange ‘head’: designed to be as inert as possible, it was made from a combination of rigid plastic and ‘fibrecrete’ – a cross between fibreglass and concrete. It's still widely used in buildings where complex architectural shapes are required. The whole head could also be rotated relative to the main enclosure, and controls to the rear enabled adjustment of the treble and midband levels to suit the space in which the speaker was used.
What’s also no surprise is the speed with which the 801 was adopted by music enthusiasts and professional users alike, thanks to its combination of superb sound and pro-friendly features such as built-in overload protection. This monitored the voltage to each driver and cut the power when ‘safe operating levels’ were exceeded, complete with a push-button reset to get the speaker – and the user – back to work.
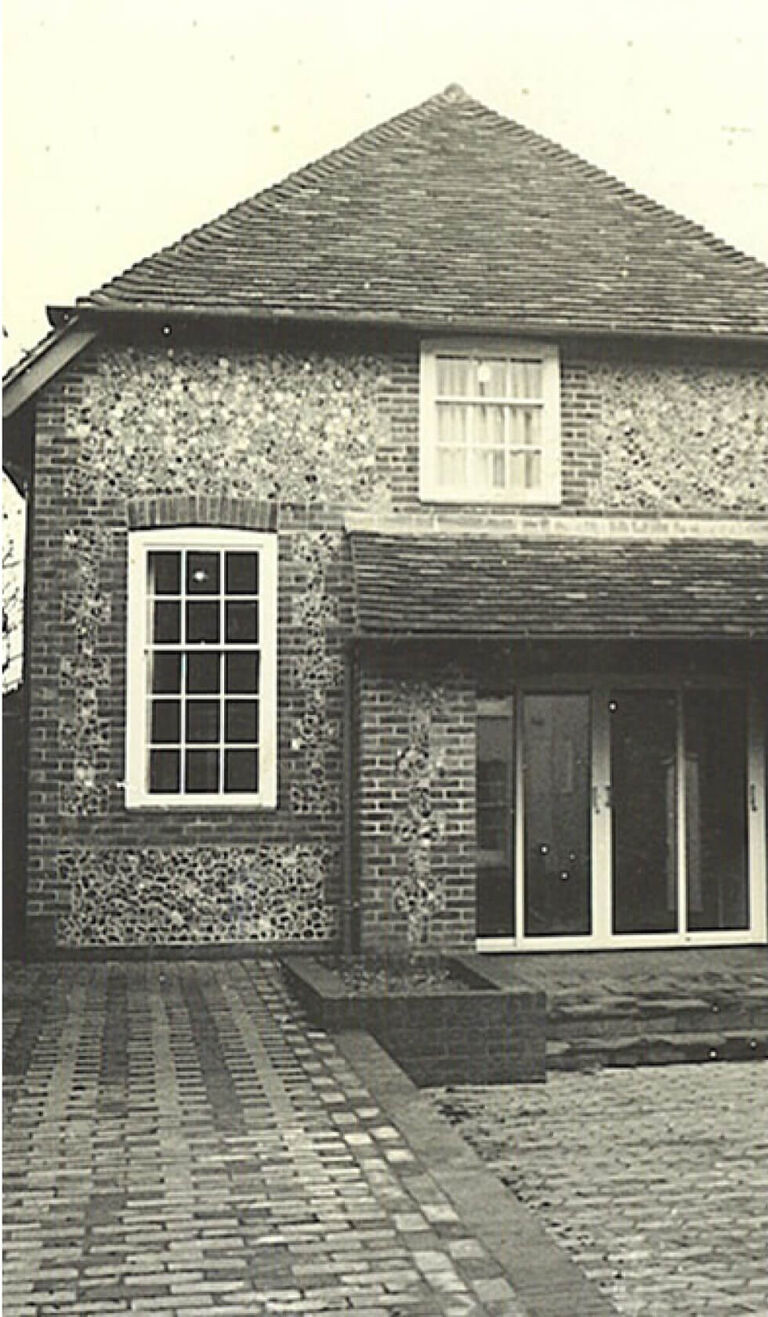
Steyning Research Establishment
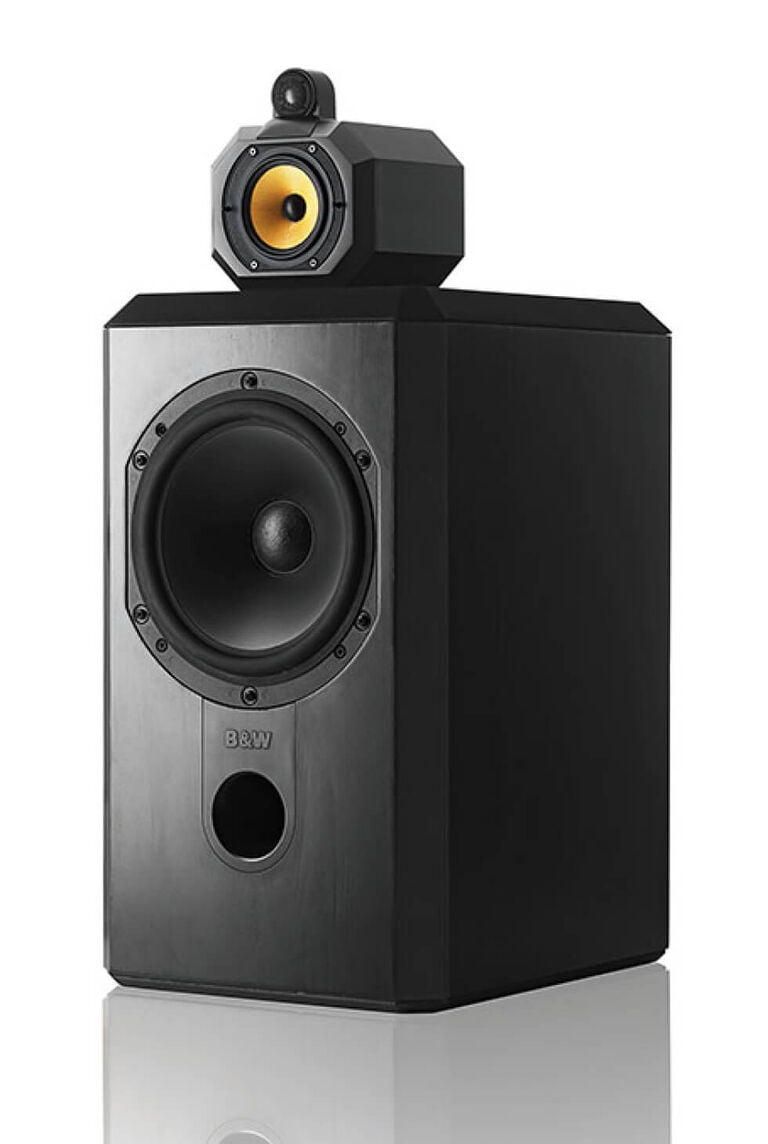
Matrix 801
The breakthrough moment for the 801 came when EMI adopted it as its reference monitor at Abbey Road Studios, leading many other facilities around the world to follow suit. A contemporary picture shows a pair of 801s – all 47kg apiece of them! – mounted on tall open-frame stands in the studio, and this co-operation between Abbey Road and Bowers & Wilkins – and the ongoing installation of successive generations of 800 Series speakers – continues to this day, as does their use in many other world-leading recording facilities.
The 1980s saw an even greater focus on research and development at Bowers & Wilkins, with the celebrated Steyning Research Establishment (or SRE) being founded just a year after the 801 was launched, and going on to form the backbone of the company’s R&D for almost four decades, before being replaced with the much larger Southwater Research Establishment – so still SRE! – in 2019.
Steyning was always about pushing the limits of speaker engineering, and from its work came innovations redefining the 800 Series. For example, the Matrix 801, launched in 1987, tackled the entire subject of cabinet rigidity and vibration with an internal bracing structure formed from a lattice of interlocking spars, stiffening the entire enclosure in three dimensions. Still recognisably an 801 speaker, although now with a front-venting bass port in place, the Matrix 801 would go on to set the blueprint for the construction of all Bowers & Wilkins speakers, in which use of the Matrix system is widespread. Oh, and the bass driver was growing: it was now a full 30cm unit, giving the speaker low-end extension down to 20Hz. As one reviewer commented, it was like having ‘a pair of speakers with perfectly aligned subwoofers built-in’.
While the Matrix 800 went through a series of iterations in the following decade, not least including its development into a complete speaker series from the little standmount 805 through to the flagship 801, even more radical changes were being plotted behind the closed doors in Steyning. A hint of what was going on – well, a jaw-droppingly spectacular hint – of what was happening arrived in the form of the sculptural Nautilus in 1993, its form reflecting the concept of damped tubes to control the output from the rear of its drivers, the bass section curling like the aquatic creature from which it takes its name.
A design classic? Definitely, and one that’s still being made by hand in very limited numbers, alongside the 800 Series Diamond speakers in the Dale Road factory in Worthing, UK. But Nautilus was more than just a striking one-off: the technology behind it was to influence the design of the company’s whole range, as was evidenced when the Nautilus 800 Series appeared five years later.
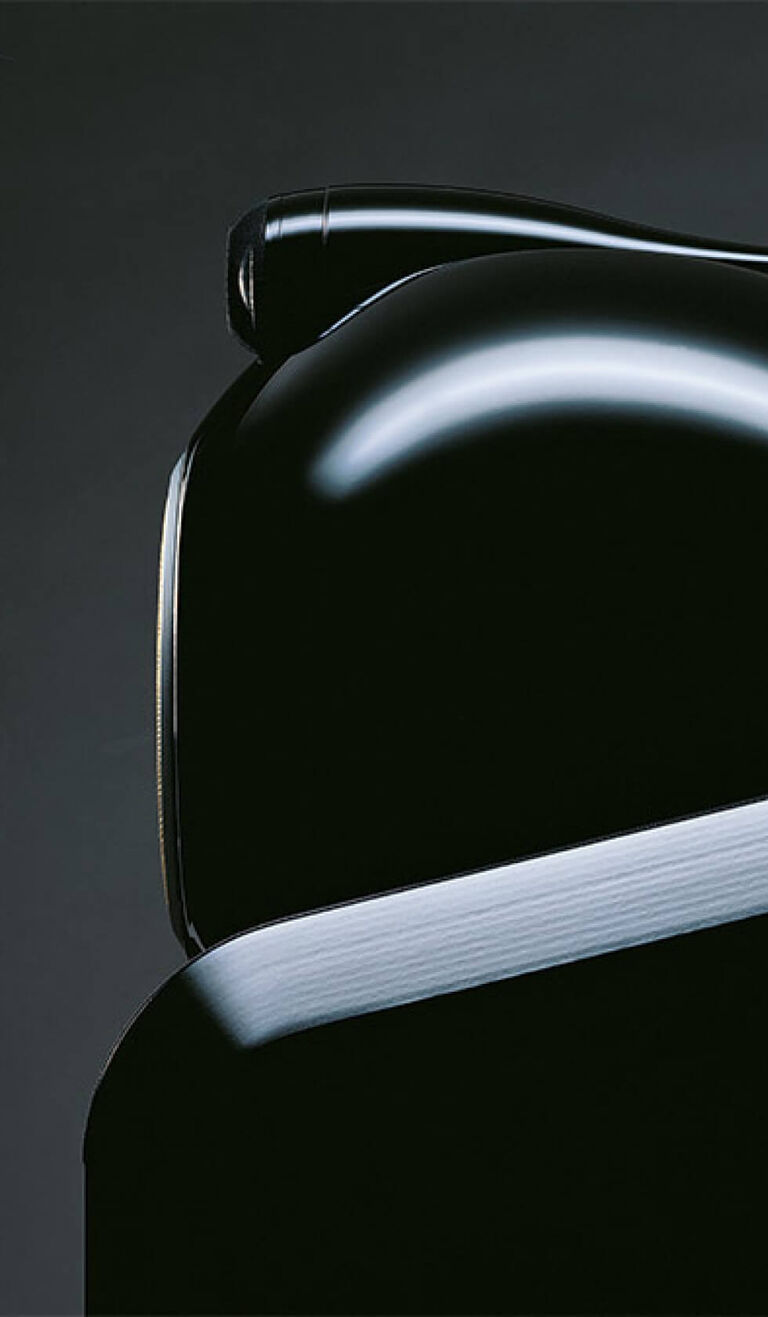
Nautilus 800
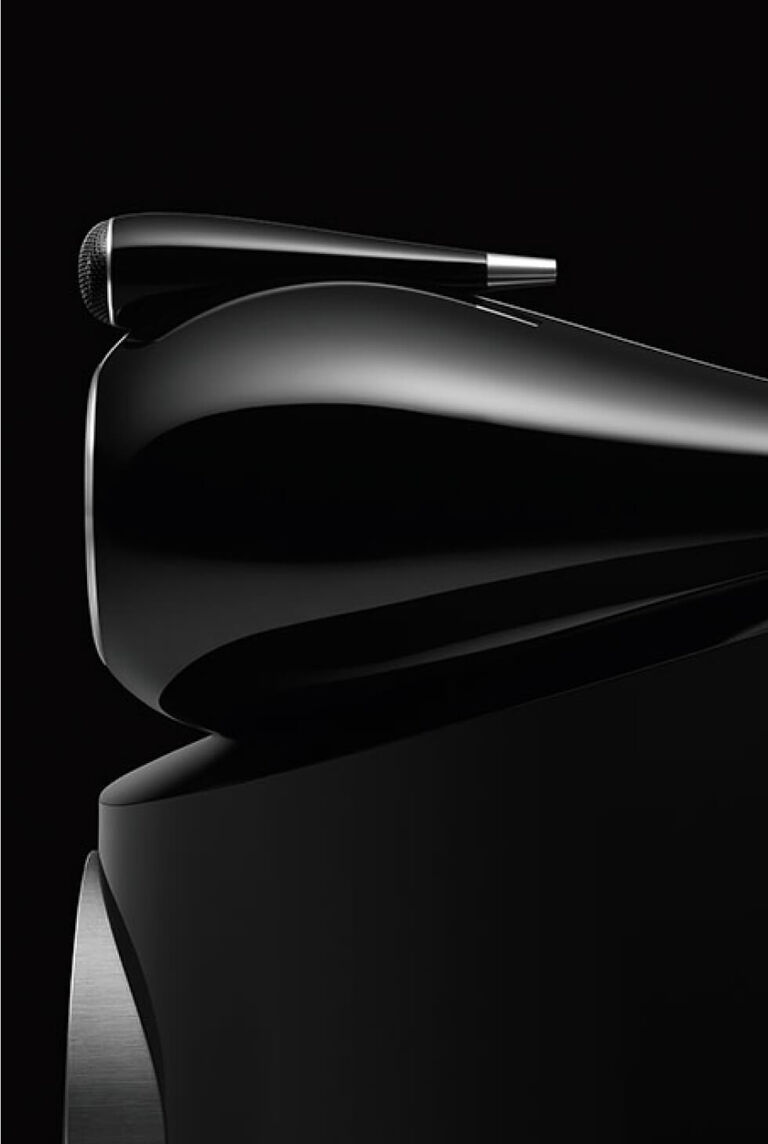
800 D3
Yes, the speakers were recognisably descendants of the original – but only just: the main enclosure gained a softer, curved form, complete with a downward-venting bass port, and on its shoulders sat a near-ball-shaped head containing the midrange driver, seemingly hunkering down into the bass unit and made from Marlan – another of those materials more commonly found in the construction industry: think all-in-one ceramic-look sinks and drainers.
Atop that was a separate tweeter pod, closer resembling the ‘Tweeter-on-Top’ pods of the 1970s, but here elongated out to the rear to form a ‘Nautilus tube’. Also presaging what was to come later, the speaker sat on a hefty cast-metal base, down onto which the Flowport vented, and inside which were the crossover components, suitably isolated from the powerful bass on offer from the paper/Kevlar composite 38cm bass unit of the Nautilus 801, or the dual 25cm bass drivers of the flagship Nautilus 800.
By now, the speakers were somewhat heavier than the original 801, the Nautilus 800 being 125kg apiece and heading a complete range, all the way down to the compact Nautilus 805, the slender Nautilus SCM1, and a brace of matching centre speakers for multichannel use – and all with that Nautilus tube tweeter.
Next up was another remarkable breakthrough: a tweeter dome formed by chemical deposition of diamond material, the Steyning team having identified this as the optimum tweeter material for rigidity and lightness. These diamond tweeters were so revolutionary in their performance – offering a first breakup frequency of over 70kHz – that they gave their name to the original 800 Series Diamond of 2005, which were supplanted in 2010 by a range of upgraded ‘D2’ specification models.
Then, in 2015, it was time for the next major breakthrough: the new 800 Series Diamond, or D3 – announced that ‘From drive units to cabinet geometry, every major component has been rethought and reinvented.’
In fact, everything, give or take the odd screw, was all-new. The ‘Turbine’ head housing the midrange driver was now made from solid metal, while the tweeter ‘pod’ was also milled from solid aluminium, while the cabinets of the uppermost models – the 800, 802 and 803 – took on a much more sculptural shape. It’s formed using the Worthing factory’s ‘Reverse Wrap’ technology, in which multiple layers of beech are pressed together under heat to form the front baffle and sides of the enclosure in one piece for greater stiffness, then joined at the rear with a metal spine, further bracing the cabinet (along with the internal Matrix) and acting as a heatsink for the crossover components mounted to it.
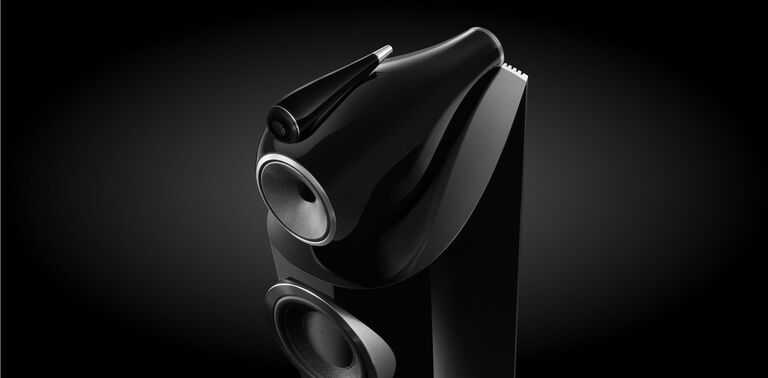
The drivers in the D3 models were also new: the tweeter is a refined version of the Diamond dome, and the midrange Continuum cone made from a woven material developed in-house, and finally replacing the yellow Kevlar-cone drivers seen in models all the way back to the original 801. And the bass? Well, that’s in the hands of composite Aerofoil drivers, so-called due to their wing-like cross section: there are two 25cm units in the 800 D3 flagship, allowing it to deliver bass all the way down to 15Hz, aided by downward-venting Flowport technology.
The 2015 launch announcement for the D3 series said that ‘The 800 D3 is driven by technological innovation. And the rulebook for loudspeaker design has been ripped up and rewritten in the process. The future of loudspeaker technology starts here.’
Six years on, the future’s only just beginning…