The Legacy of Vinyl – Exploring Music’s Most Treasured Medium: Part 1
Music is simply more accessible and shareable now than ever. Yet, despite that, vinyl buying and listening are on the rise.
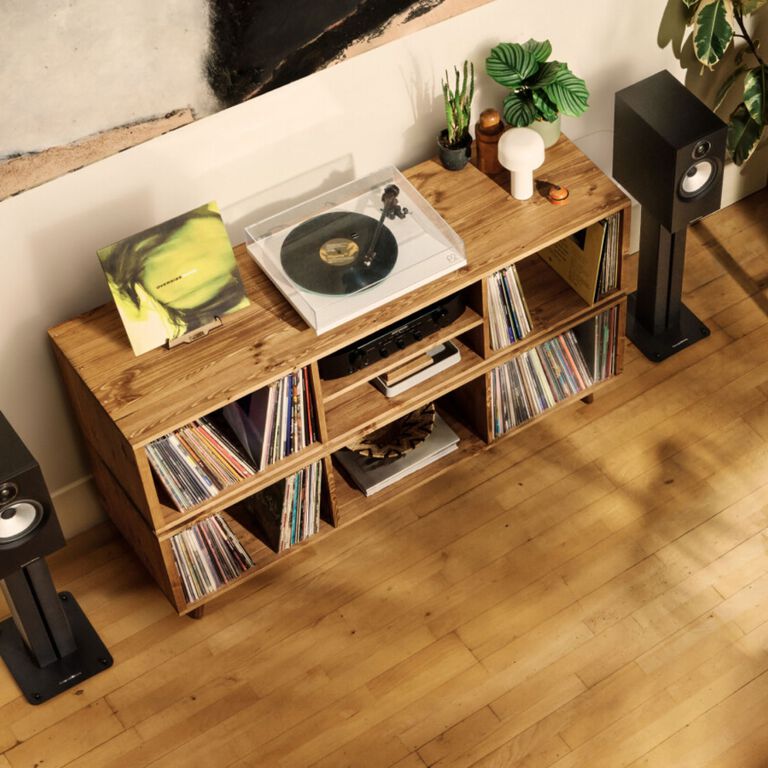
Nowadays, there are so many ways to listen to your favourite music. You might choose from one of the many digital streaming platforms like Spotify, Amazon Music, Apple Music and more to enjoy yours. However, you might still prefer to listen using physical media, such as CDs or even cassettes – but when it comes to physical media, there’s one medium that stands out from the rest for its popularity and cultural significance – vinyl.
When you think about digital listening, convenience is taken for granted. To the seasoned listeners who grew up in the heyday of vinyl, digital streaming must seem like a seismic shift. It’s like magic – any song, anytime, anywhere. Music is simply more accessible and shareable now than ever. Yet, despite that, vinyl buying and listening are on the rise. So, why is vinyl, a medium that requires such a painstakingly intricate listening routine, still having an impact on today’s musical landscape, for both younger and older listeners?
What is it about vinyl that makes it so special? Is it the warm sound and excellent quality it offers, the ritualistic behaviour of carefully removing the record from the sleeve, placing it on the turntable and gently lowering the needle into the grooves, its historical significance, or the desire to build up an impressive record collection of your own?
It could be vinyl’s uniquely sensory experience. The feel of the disc, the act of putting on your favourite record and inspecting the artwork front to back while you listen. That smell of freshly unboxed vinyl – as well as those old, pre-loved eBay collectables that tell a story much deeper than that of the musical grooves engraved on them. From the sound to the touch, smell and look of vinyl, there’s undoubtedly something emotional about our connection to them.
In this two-part blog series, Bowers & Wilkins takes a deep dive into the technical and cultural elements of vinyl, exploring the ‘how’ and ‘why’ of music’s most celebrated medium.
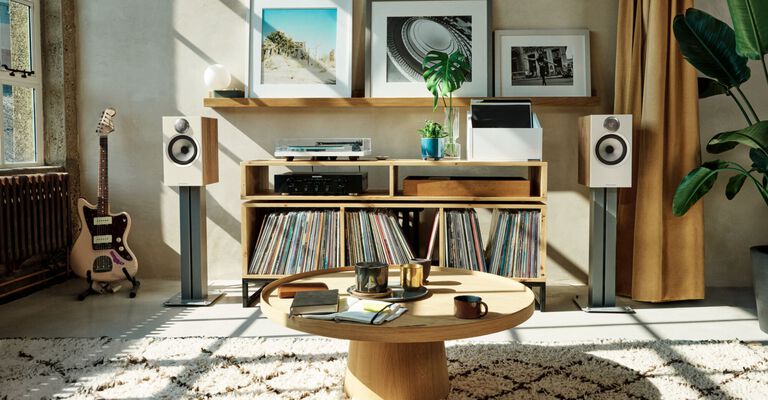
From pellets to performance
So, what exactly is a vinyl record? We all know what one looks like, but there’s much more to be said about its journey from a factory to your turntable.
To put it simply, vinyl records are a type of plastic disc that are spun at a constant speed and read by a needle that tracks each groove embedded in the plastic, each one of which contains musical information.
They’re made using polyvinyl chloride (PVC), a high-strength thermoplastic material created by combining chlorine and ethylene with additives using various processing techniques. The PVC used to make the vinyl discs usually starts as pellets, which are distributed to wherever your new vinyl record is being pressed.
Before your PVC pellets are transformed into beautiful vinyl, the manufacturers will first need a physical master of the recording that’s being pressed to vinyl – the master record.
While the master record is adapted from a digital master of the finished song, the mastering process, in general, is the final stage in creating a song or album. It requires a mastering engineer to take the final mixdown of the music in premaster format, usually between -6dB and -12dB, and add processing techniques like EQ, limitation and stereo imaging. This polishes the overall sound and allows the volume to be brought back up for streaming, CD and vinyl listening.
Expert insights
Geoff Pesche is a mastering engineer from Abbey Road Studios, and the man behind some of the world’s most famous records from artists such as Gorillaz, Kate Nash, Coldplay, Basement Jaxx, Amy MacDonald, Kylie Minogue, New Order, and others. He took time out of his hectic schedule to speak to Bowers & Wilkins about the mastering process.
According to Pesche, “mastering is the last link in the production chain that links the studio to the shop or the online retailer. So, this is the last port of call where you can alter the sound of a format before it's manufactured. We're doing sequencing, tonal balance, final editing, and, occasionally, having a row with the band!”
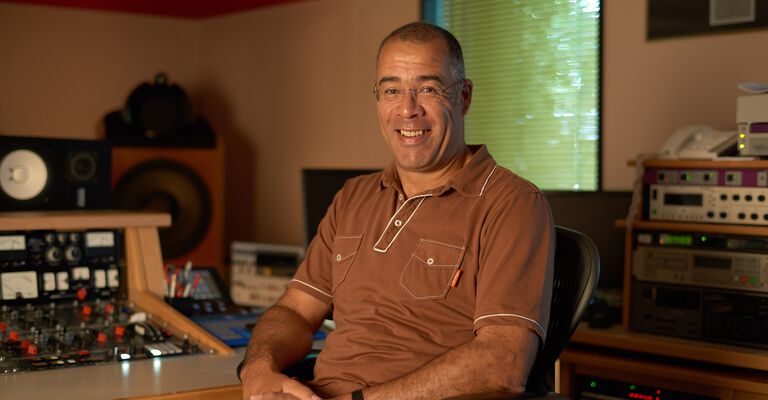
Trust the process
To create the master record for vinyl, a digital master is adapted by a mastering engineer to make sure there is no limitation on the recording and that the frequencies and sound quality are optimised for vinyl listening (and for listening on any other format).
Once the digital master is enhanced and made vinyl-ready, a blank acetate disc coated in lacquer or – more commonly in today’s industry using Direct Metal Mastering (DMM) – a copper disc, is placed on the lathe of a recording machine where a heated stylus is used to engrave the disc with the audio signal from the master recording. As one side of a 12-inch vinyl record has space for up to roughly 20 minutes of sound, the acetate or copper disc is flipped halfway through, and the process is repeated for the rest of the music to create the B side.
Following the engraving process, the lacquer disc is sprayed with tin chloride and then a liquid silver coating to help conduct electricity. It’s then submerged in a bath of electrified water and dissolved nickel so that the nickel can fill the finely cut grooves. This process creates a negative of the cutting with a metallic exterior that can be used to press all the vinyl you need. However, if you’re using DMM, this step can be skipped as the copper disc used in this process will already be conductive of electricity.
Now that the vinyl stamper is ready and a centralised hole is punched through to allow it to attach snugly to the vinyl press, it’s time to start pressing the record. The PVC pellets which make up the plastic of the vinyl are heated and merged into vinyl patties – also called vinyl biscuits – and the circular artwork seen in the centre of most vinyl records is added.
The vinyl biscuit is then placed on the vinyl press, and 100 tons of pressure behind the stamper lowers down at extremely high temperatures, pressing the negative stamper into the PVC biscuit. Once the vinyl is perfectly pressed, it’s sent to a cutting table to smooth off the sharp edges and then packaged up before being shipped off to music lovers across the globe.
Different speeds, different benefits
Vinyl isn’t all pressed to play at the same speed, however. If you’re unfamiliar with RPM, it means Revolutions Per Minute – it’s the number of times the platter on your turntable rotates fully each minute. Most vinyl records are cut for either 45 RPM or 33 1/3 RPM (and in the past, 78 RPM).
The faster a record spins, the less information it can hold, and the playtime is shorter. So, 33 1/3 RPM is the most practical for longer records and requires fewer journeys to your turntable to flip the vinyl. While 45 RPM records, usually 7-inch vinyl or 12-inch singles, fit less audio information on them as they play faster, the increased speed of the vinyl playback actually improves the overall sound quality for listening. With the vinyl playing at a higher RPM, it turns under the stylus quicker, meaning more audio information travels from the stylus to the speakers.
Again, we learned more about this while speaking with Pesche: “With a record, the inner circumference is turning slower than the outer circumference, even though turntables go at a universal speed,” he explains.
“With a record, you get what's called the pinch effect in the middle of the record. Because it's turning slower, the response from the pickup will decrease and will not be as good as the outer circumference. So, at 45, obviously, it's going to be better.”
In addition to the commonly used 33 1/3 RPM and 45 RPM, the first records were cut at 78 RPM. This catered to the old phonograph players where a crank was hand-turned to spin the vinyl. The average user was believed to turn the crank at around 80 RPM, hence the use of 78 RPM.
Although there are different record speeds to factor in, trust that the engineer behind the record has made the best choice for the artist so their music can be delivered as close to the original recording as possible
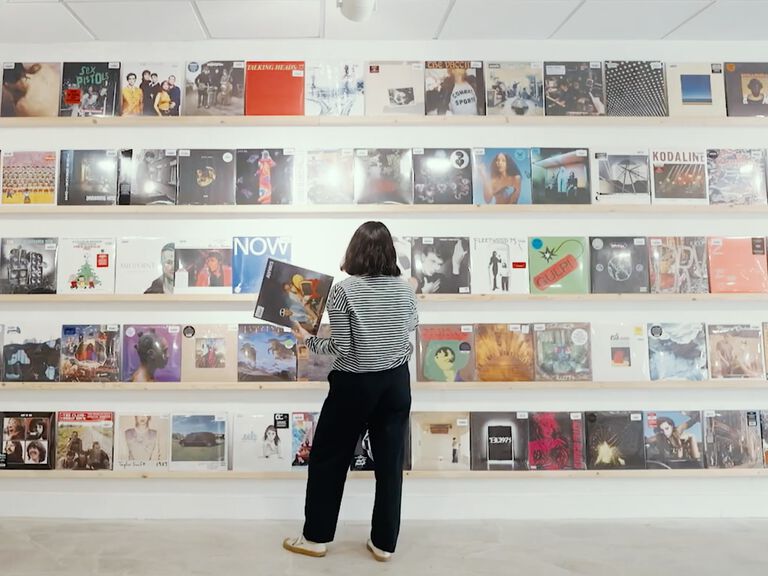
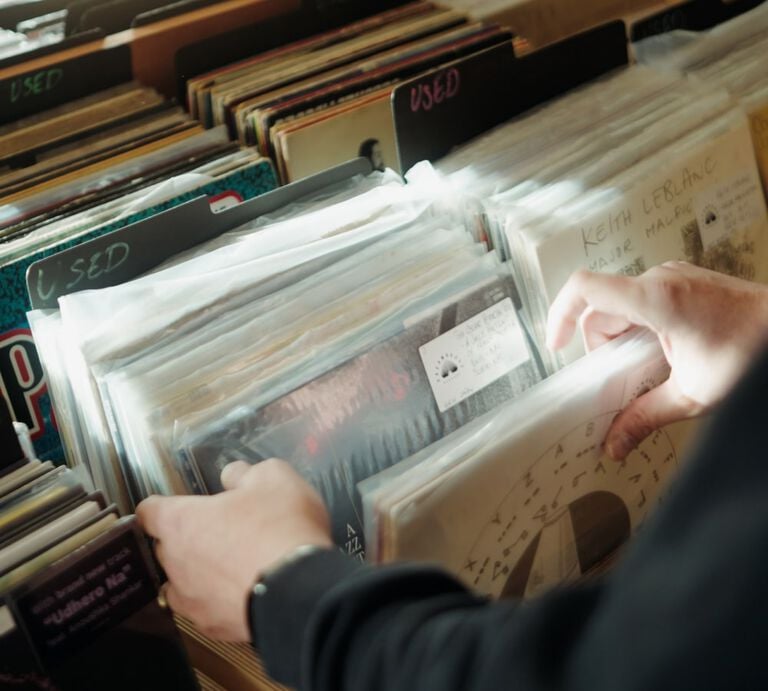
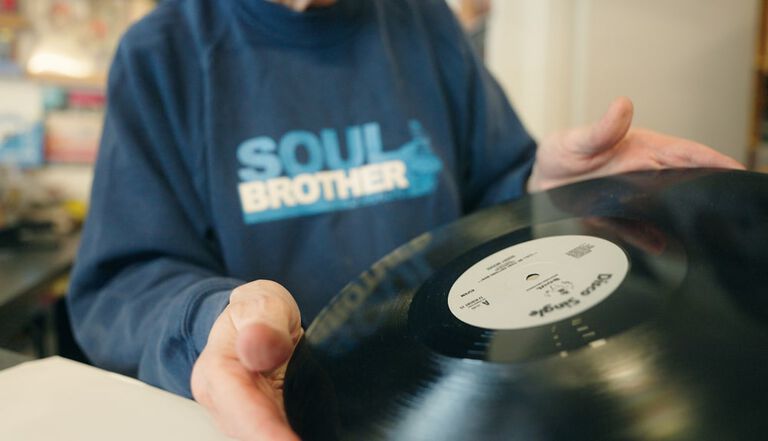
Hold on, weight a minute
Much like the different RPM specs that vinyl is pressed at, you’ll probably have noticed that different weights of vinyl are also available. The standard vinyl weight is between 120 and 140 grams, but the heavier 180-gram vinyl is also available – and the go-to for some.
Many think the significantly thicker 180g vinyl provides better bass, more detailed high frequencies and reduced noise. While this is true for most 180g pressings, it’s not necessarily reliant on the weight of the record. The truth is that companies usually give more care to the overall manufacturing process of 180g pressings, sourcing better material for the vinyl, such as cleaner masters of the original recording.
Pesche gave us some insights into whether it’s really as important as some think, explaining that “What you really need is a flat pressing. You need one that doesn't warp. And some of the lighter ones don't warp if you look after your records, but people think that bigger is better.”
That being said, there are benefits that 180g records offer. They’re stronger, which reduces the likeliness of them breaking or warping, and the additional weight makes for a more secure platform for the stylus to sit on.
Vibrant vinyl or classic black
Back in the early days of vinyl, black-coloured records were the only option available, and, luckily, they offered great audio quality. The black pigment in the PVC helps the vinyl absorb unwanted noises and hiss, making it the most practical option for manufacturers and listeners. For many years, coloured vinyl was less prevalent, and although it looked more interesting, the dyes and pigments added to the PVC that provide those vibrant colours could cause the vinyl to warp, produce noise and feature other imperfections.
However, as technology advanced, manufacturers were able to produce vinyl without these issues thanks to higher-quality pigments and dyes and modern pressing techniques that avoid unwanted warping. So, whether you prefer classic black vinyl or you’re a fan of the multi-coloured equivalents, you don’t need to worry about compromising on sound quality. Good news for collectors who love the exclusivity of limited colour presses and adding those coveted special editions to their arsenal of records.
As well as the now-popular coloured vinyl, you can even get vinyl with specific images on them – these are called Picture Discs. Created by sandwiching a printed image between two layers of clear vinyl, Picture Discs are more visibly striking than regular black or coloured records, but they have their disadvantages. Housing something between two layers leaves little room for mistakes. If there is even the slightest uneven surface, it can cause the vinyl to warp – and even the smallest level of warping can be detrimental to the sound quality. So, if great sound is your top priority, rather than pretty Picture Discs, it’s best to stick to classic black or newer coloured vinyl.
From records to high-resolution
Now that we’ve covered the basics of what vinyl is and how it’s made in its many forms, it’s important to explore how it works to deliver high-resolution sound. To play vinyl, you’ll need a few essentials: a turntable, preamp, amplifier, speakers – and an isolation platform if you’re worried about vibrations from the surface your turntable sits on.
Although the way vinyl works is universal, what you use to play it will impact the quality of your listening experience. So, if you’re passionate about great sound, investing money and time into a decent setup will help you get more out of your records in the long run. In other words, the care you put into your listening setup will be reinforced by your enjoyment of beautiful sound.
The way records work has remained largely unchanged since the days of phonographs and gramophones. Once the vinyl is placed on the turntable, a diamond-tipped needle, known as the stylus, is carefully lifted and dropped onto the first outer groove of the vinyl.
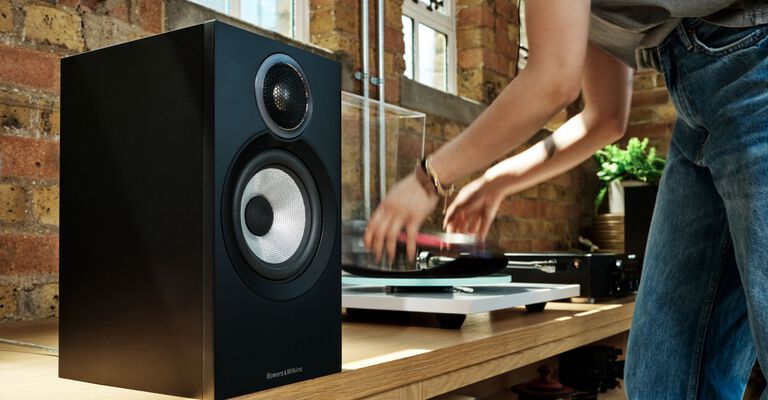
Setup is everything
First things first: your record player needs to be set up on a level surface that is free from vibration. This is especially important if you live in a house with a sprung wooden floor. A wall bracket or an isolation platform for your turntable can be essential add-ons to get results here; if not, there’s a risk that your records might constantly be skipping in sympathy to the vibrations that are travelling through the floor into your turntable.
Next, it’s essential to get the tracking force of your stylus perfectly balanced. Tracking force is essentially your needle’s weight, and you want to make sure it has enough force behind it to sit within the grooves and accurately track the audio information on the vinyl as it plays.
The counterweight on the tonearm can be adjusted to provide your needle with the perfect weighting for optimum performance. By doing a quick Google search or checking your turntable’s manual, you’ll likely be able to find the suggested weighting for your counterweight. Correct tracking force will ensure your needle doesn’t bounce during playback, keeping your records in better condition and delivering your music with precision and accuracy. It’s important to note that all record players are different in this respect and offer wildly varied levels of complexity.
As the turntable spins the record, the stylus moves across the grooves, which hold the audio information from the master record. The left side of the groove provides the left side of the sound, and the right side provides the right sound, so that’s another reason you’ll need your needle tracking correctly. This movement causes the needle to vibrate, sending these vibrations up the cantilever to a cartridge, a type of electromechanical transducer which houses a magnet situated between two coils. The left coil and right coil are used to send electronic signals from the left and right channels, and as the magnet vibrates, it moves between these coils to deliver a stereo signal.
The phono stage is key
The signals from the coils are sent up the record player’s tonearm and into the wiring of the turntable. This is where the phono stage – or, put more simply, the preamplifier, comes into play. At this stage, the signal from your record is incredibly quiet, so it needs more power. The preamplifier connects your turntable to your amplifier and boosts the signals for more amplification. Some of today’s record players have in-built phono stages, which is great for the entry-level vinyl listener, but for those who love to hear the nuances in their music with even more detail, an external phono stage or a high-quality phono stage built into your amplifier often provides better quality, high-resolution sound from your vinyl records.
Once the signal reaches the amplifier, it’s boosted further and separated between the left and right channels, allowing your left and right speakers to deliver stereo sound. The audio signals from the amplifier are converted by the loudspeaker’s transducer, preparing them for output. The speaker cones then vibrate, moving forwards and backwards to pump out the soundwaves we hear as music.
To summarise, the way vinyl works hasn’t changed much, but now, with all of the exceptional audio technology on offer, there are ways you can make the most of your treasured records – you’ll need to spend some time setting up your perfect hi-fi system and keeping your records and equipment in good condition.
Good habits, happy records
Caring for records is an essential part of every vinyl lover’s life. Clean records last longer, sound better and look more appealing, and if you’re in the market to sell some of your collection, be it to upgrade your setup or buy more records, you’ll likely fetch a higher return for well-cared-for records.
Keeping your records dust-free is an excellent place to start. Carbon fibre brushes are great for this – and recommended by vinyl experts. The carbon fibre bristles are extremely fine and help remove tiny dust particles from the vinyl grooves as well as static electricity. Clearing the dust will not only make your vinyl shine but prevent any unwanted pops or crackles when listening, as your needle will enjoy better traction to the record.
When storing your records, whether in alphabetical order, organised by genre, year, or colour – or for fans of the movie High Fidelity, autobiographically – keeping them upright in their sleeves in a dry, cool place with some breathing room between them ensures they don’t get crushed or warped. Again, this level of organisation and care will result in your records sounding better for longer – and make them easier to find.
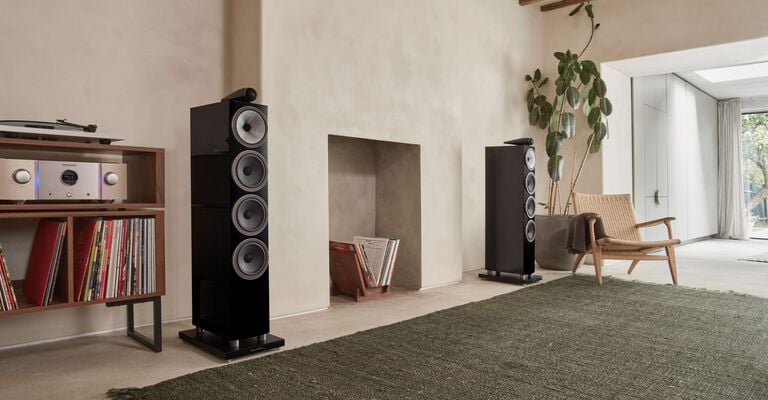
Caring about sound
As important as it is to keep your vinyl in good shape, caring for the setup that plays your records is essential for both listening quality and vinyl longevity. If dust is trapped on the stylus of your record player, it can cause interference when connecting to the grooves on your vinyl, impair playback quality and damage records in the long run. You can keep your stylus clean by using a stylus brush to gently remove dust or, from what seems popular in the audio community, an Onzow Zerodust Stylus Cleaner, which uses an ultra-soft gelatinous pad that removes debris from the stylus tip. It makes perfect sense – care for your kit, and it’ll last longer.
Of course, clean is good when it comes to equipment and records, but buying a decent turntable and setting it up correctly is another crucial ingredient for excellent sound. “Buy the best turntable you can afford,” says Pesche.
“You must have your turntable set up properly. You can buy an expensive turntable like a Rega Planar 8 or something, but if it's all wonky, a Pro-Ject turntable for a few hundred quid is going to sound better,” he explains. “Spend a few bob on a turntable and get it calibrated. The other bits you can chop and change, but if you buy a decent turntable, it'll last you forever – if you're careful with it.”
New life for old vinyl
It’s fascinating to think that vinyl almost vanished from the mainstream when CD – and then streaming – took the spotlight. But now, with the boom in record buying, collecting, and manufacturing, more time and effort has been dedicated to the vinyl cause. To support the resurgence in vinyl listening and the culture surrounding it, many engineers and manufacturers have adapted their processes to cater to the modern music lover – and their desire for the best in sound quality.
Stay true to the tapes
You may have come across the term ‘remastered’ when skimming through classic records online or in-store. This essentially means a sound engineer has used modern techniques and new insight into the process to refresh a timeless song or album. It’s a great way to add new depth and clarity to the music. When it comes to remastering, according to Geoff Pesche, the source material and staying true to the original master tapes is essential.
“The key with remastering is the source material. If you can find the right source material, you can go back to the bricks and remaster it properly,” he says.
Speaking about his experience remastering, Pesche explains: “I can respect the master tapes from back then because it would be easy to just think ‘oh, we're in the 21st Century now, let's turn all the treble up, let's turn the bass up.’ Well, that doesn't respect the original record, does it?”
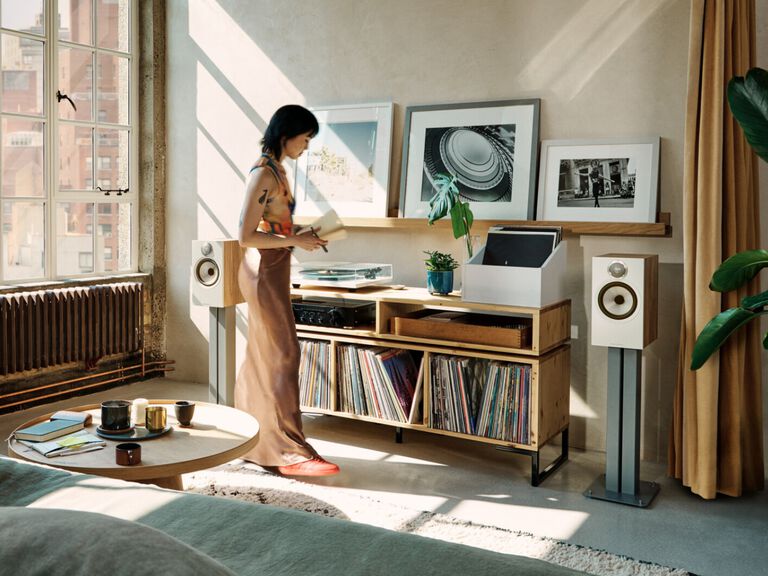
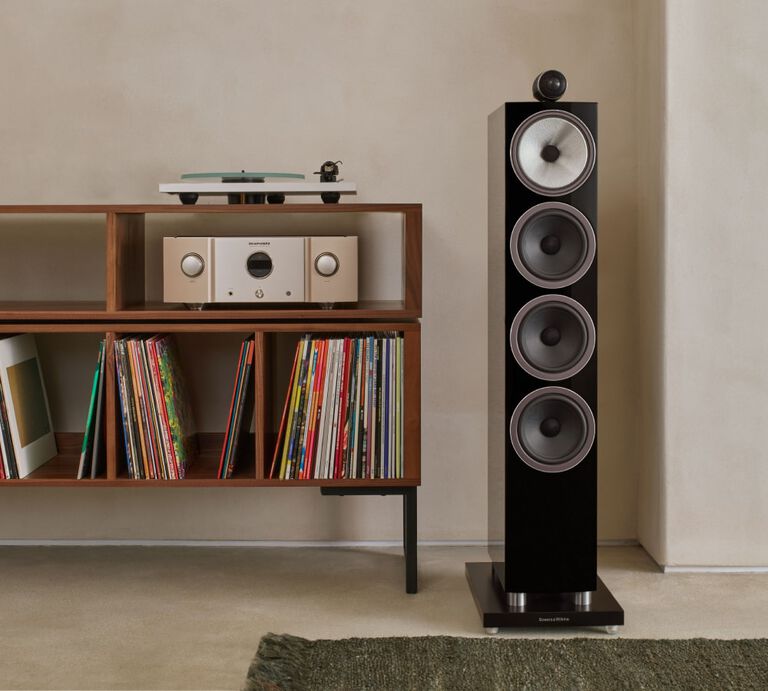
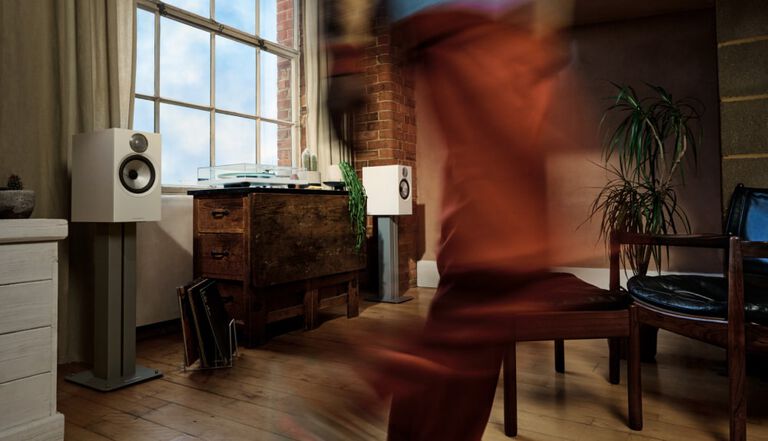
Half the speed, double the quality
Half-speed mastering is one of these quality-enhancing processes, and although it’s pretty popular now, when vinyl was in its early years it was pretty rare. Half-speed mastering dates back to the 1960s when British record label Decca Records implemented the process to improve the dynamic range and frequency response of their vinyl records. Just as it sounds, half-speed mastering uses the same initial vinyl-cutting process, but each part of this process is slowed down to half-speed to help create a more detailed master record.
But let’s let the experts give some insight into this. Speaking to us about the half-speed mastering process, Pesche explains: “The principles are great. The high frequencies on records are the most difficult to cut. It's easier to cut a signal at 1000 kilohertz than it is to cut something at 16,000 kilohertz, so if you half the speed of the signal, all of the time components – the cutter head, the cutting rack, everything – are now using half the power. So it's working 50% less hard.”
So, when put into practice, your digital master is played back at half the speed while the cutting lathe etching the audio information onto the lacquer disc or copper disc also runs at half the speed. This allows double the amount of audio information to be etched into the lacquer disc, resulting in more accurate, cleaner sound when played back on your record player.
While this is a tried-and-tested method of improving sound quality, half-speed mastered versions of original pressings help revive old recordings and enhance their exclusivity. It’s more time-consuming and costs a fair bit more for manufacturers, but the great sound quality, coupled with new artwork and any exclusive bonus material, provides the perfect collection of features for special edition releases that vinyl lovers crave.
Reviving the classics
In addition to remastered and half-speed mastered versions of vinyl, sound engineers are often enlisted to add their magic touch and technical prowess to the mixdown of a previously released track or album. This is remixing – not to be confused with the art of making a remix of a well-known track. This type of remixing focuses on the individual elements of the tracks, aka stems, such as vocals, bass, drums and more, refining how each part of the song sits together in the overall mix. Tweaking the frequencies of these individual elements, using new tools and techniques, can enhance the overall sound of the record, making different parts of the mix cut through for a cleaner, more sonically balanced sound.
It's techniques like this that bring us closer to the music we love, and like with half-speed mastered editions of vinyl, remixed versions are also highly sought after for precisely this reason. Take Giles Martin’s remixed version of the classic Beatles album, Let It Be, for example. Giles, the son of the Beatles’ original producer, George Martin, reworked the record with an all-new stereo mix featuring a mixdown specifically for Dolby Atmos. This coveted version of the album was released as a CD and vinyl special edition, featuring a book of session notes, photos and essays from Paul McCartney – as well as an EP of unreleased tracks.
It's clear that although many of these remastered and remixed records that come with a wealth of exclusive features are a sure-fire way of re-releasing and selling existing records, they do actually benefit the listener with optimised quality and also serve as exclusive showpieces for their record collection.
Record retrospective
The world of vinyl is unique. From its intricate production and listening processes to its historical and cultural significance, there’s so much to marvel at. The fact that more people are getting into vinyl listening – and opening record shops of their own – in the digital age of music speaks volumes to its importance in the musical space. With every song and every album at our fingertips, we still gravitate towards physical media and the ritualistic habits that it enforces, and there’s no sign of this slowing down.
We’ve covered the 'how' and 'what' of vinyl – and, in our next in-depth look at vinyl, we’ll look at the 'why', delving into what makes vinyl and the culture that surrounds it so unique, emotional – and lasting.
Browse some of our related articles
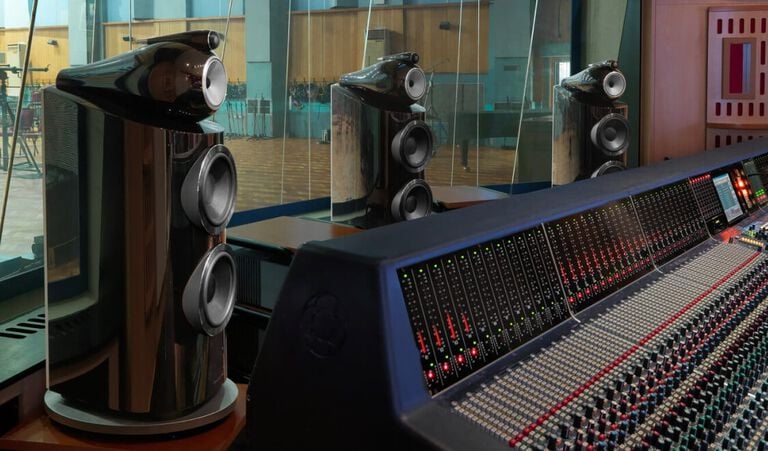